Written by Justin Gouthreau | Manager of Engineering Business Development
As seen featured in Environmental Science & Engineering Magazine’s (ES&E) June 2023 Issue
The Humber Treatment Plant was originally constructed in 1960 and is Toronto’s second-largest wastewater treatment plant. It services approximately 680,000 residents with an annual capacity of 473,000m3. The facility has undergone extensive upgrades to improve air quality and odour issues, including the biofilters.
The biofilter system consists of a group of concrete tanks which contain biofilter media. Air collected from various locations and buildings at the plant is pumped into the tanks, via a series of ducts, and filtered by the media to reduce odour and emissions.
A recent inspection at the plant determined that the biofilter media had reached its end of life and required replacement. During the removal of the biofilter media and tank clean-out, it was decided to improve the integrity of the containment. This involved the installation of a geomembrane lining system within the tank, as an added level of protection against any leakage.
Installing a geomembrane liner in a critical containment application within a square concrete tank with corners is particularly challenging and complex. This geomembrane installation required experienced installers who followed a strict installation protocol and QA/QC program.
The contractor working on behalf of the City of Toronto reached out to Layfield for recommendations for a suitable geomembrane to contain the biofilter media in an exposed tank application. Layfield’s installation team conducted a field evaluation and recommended GeoFlex™ 60 mil (1.5 mm) polyolefin geomembrane as the most appropriate for the application to line the three concrete biofilter tanks.
Each biofilter tank measures 8 m x 5 m x 1.4 m. The geomembrane’s prime-grade resin and antioxidant formula provide excellent chemical and UV resistance for the required application. In addition, the selected specialty geomembrane provided a high degree of flexibility and elongation to allow for a more efficient installation within the tank edges, corners, and around penetrations.
The installation team lined the concrete biofilter tank with a continuous layer of conductive geotextile, while overlapping the seams to create a continuous conductive surface. Following installation of the geotextile, the geomembrane’s seams and penetrations were fusion welded, and the liner was mechanically attached at the top of the tank, using a typical mechanical attachment consisting of an SS316 ¼” x 2″ bar and gasket.
Pipe penetrations within the tank were flush-mounted, which presented another challenge as typical pipe boots to seal the penetrations would not be appropriate as they required an exposed piece of pipe to seal around. As a remedy, the installers created a picture frame attachment to seal the liner around the flush pipe penetration and it was compression fitted to the tank to create a dependable seal.
To help ensure there were no leaks in the installed geomembrane, the owner chose to perform an electric leak location survey (ELLS). This was facilitated with Layfield’s Geovolt® geotextile, which provided a conductive layer beneath the non-conductive geomembrane. This allowed the ELLS to find even the tiniest holes. During the ELLS, the technician places a voltage across the geomembrane and identifies any areas where the current flows through the geomembrane, thus identifying a leak.
A variety of leak location techniques can be considered. The Arc Test Method D7953 was chosen for this installation as this method is most appropriate for clean, dry, uncovered geomembranes. During the survey, one electrode is connected to the conductive geotextile below the liner, and a second electrode with high-voltage DC power is introduced above the liner. Where a leak occurs, the circuit is closed, and an arc and audible tone is created to notify the operator of the leak. Arc testing is a reliable and accurate method that can detect leaks smaller than 1 mm in diameter.
To validate the testing procedure, the inspector created an artificial leak within the liner to verify the testing equipment would detect it.
Once the conductive geotextile is installed, it gives the owner flexibility to conduct leak surveys again in the future as part of inspection and maintenance programs. As a secondary function, it also provides a protective layer between the geomembrane and the concrete surface. Layfield’s team installed the conductive geotextile and the polyolefin geomembrane within five days. The decision to use the flexible 60 mil geomembrane saved time on the installation and made detail work in the tight corners easily accomplished.
The conductive geotextile performed well, allowing for an efficient and reliable electronic leak inspection. The biofilter rehabilitation at the Humber Wastewater Treatment Plant demonstrated how two innovative geosynthetic products could work together to deliver reliable containment solutions for wastewater treatment facilities.
To learn more about Electrical Leak Location with GeoVolt®, please be sure to check out our on-demand webinar.
Related Articles
View All News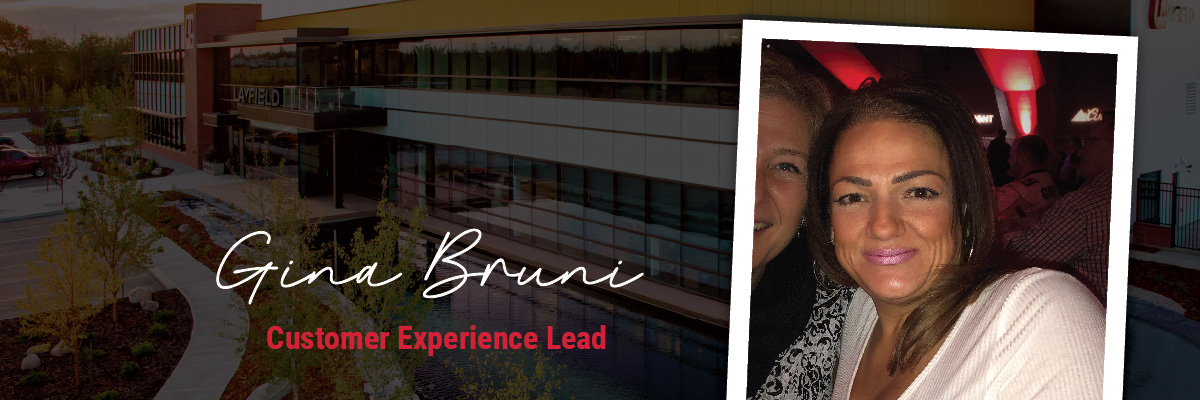
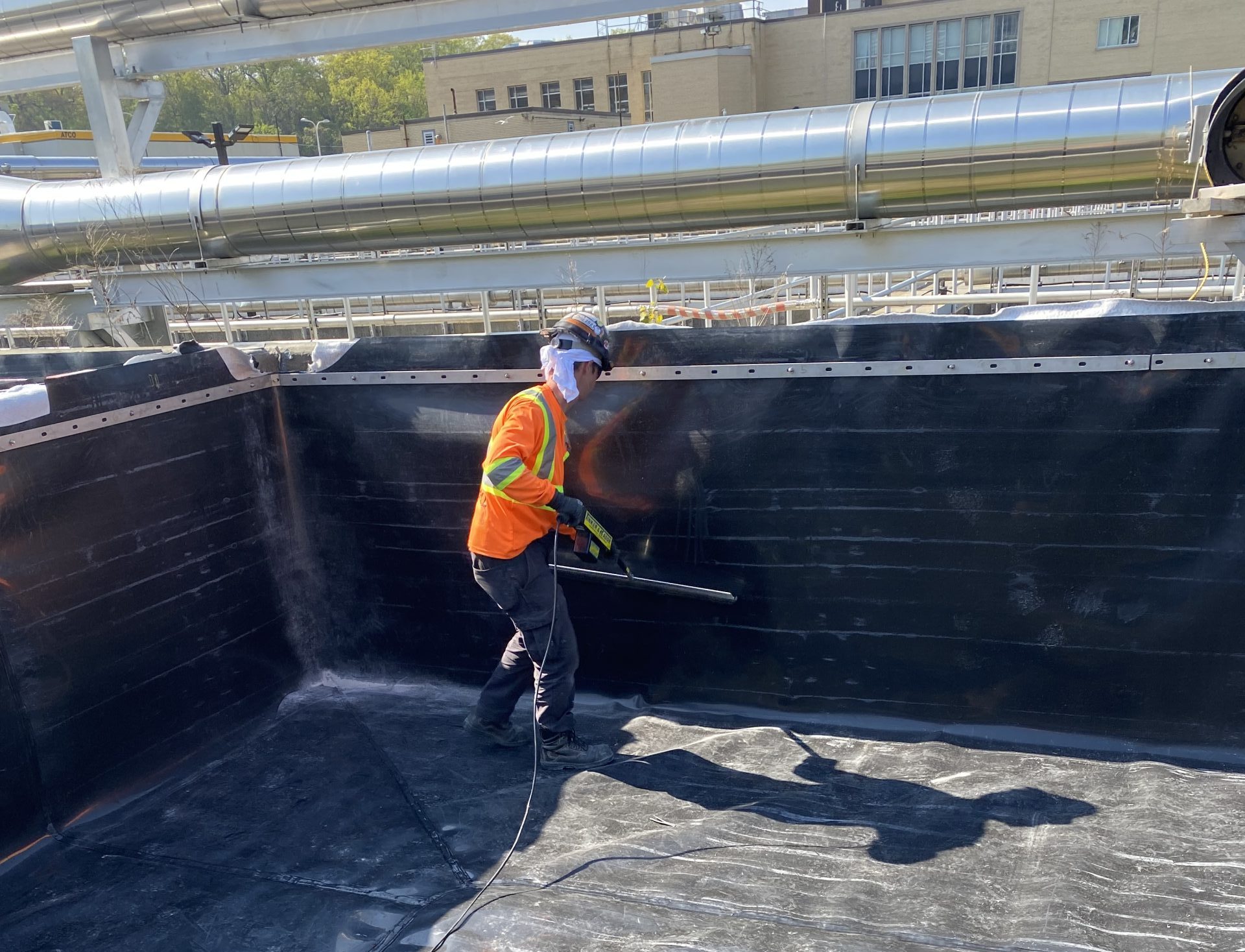
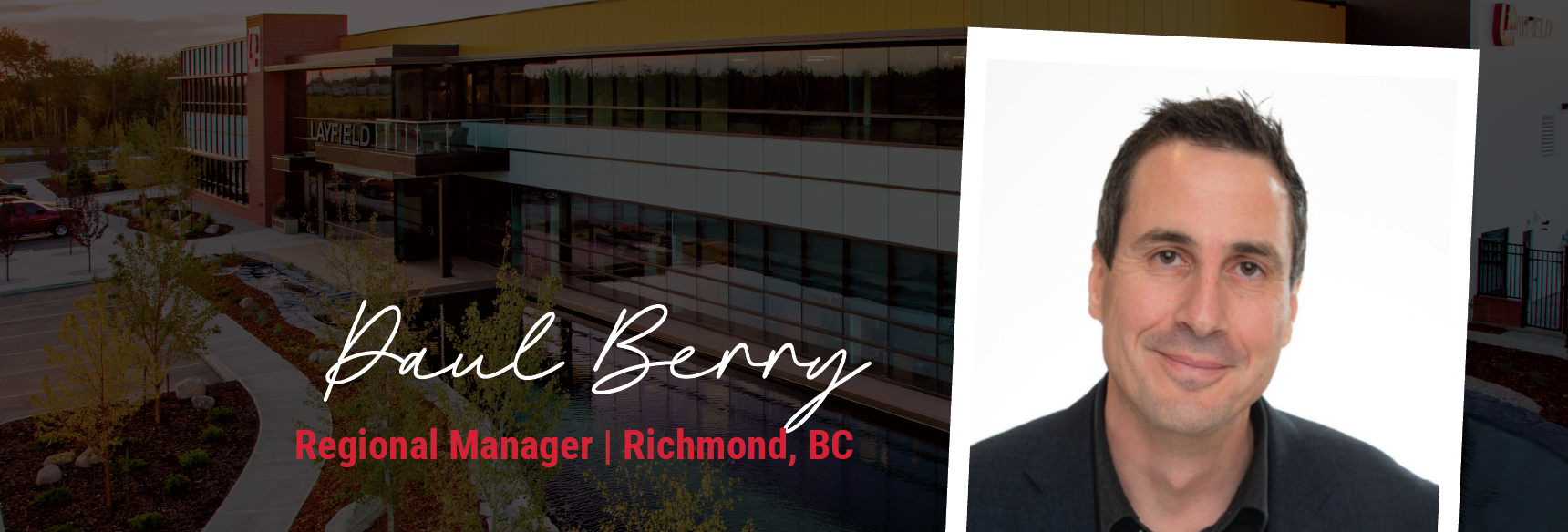
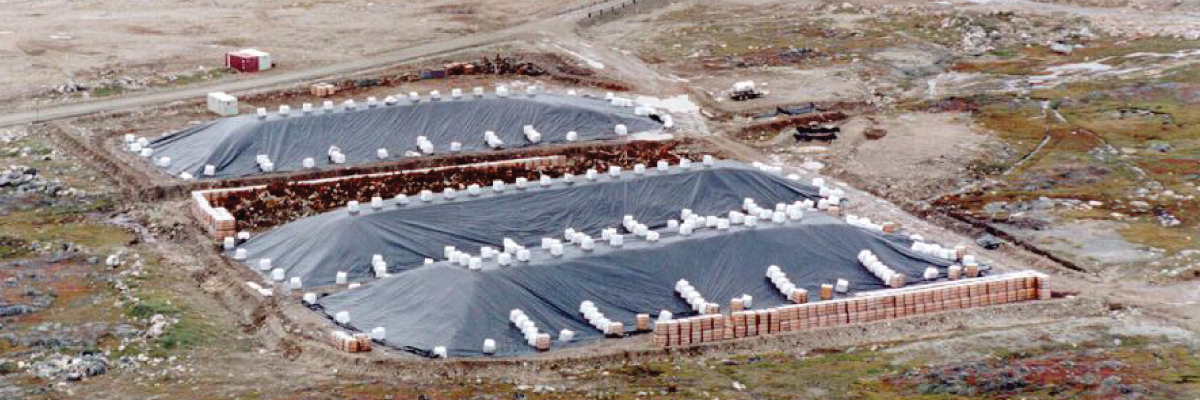
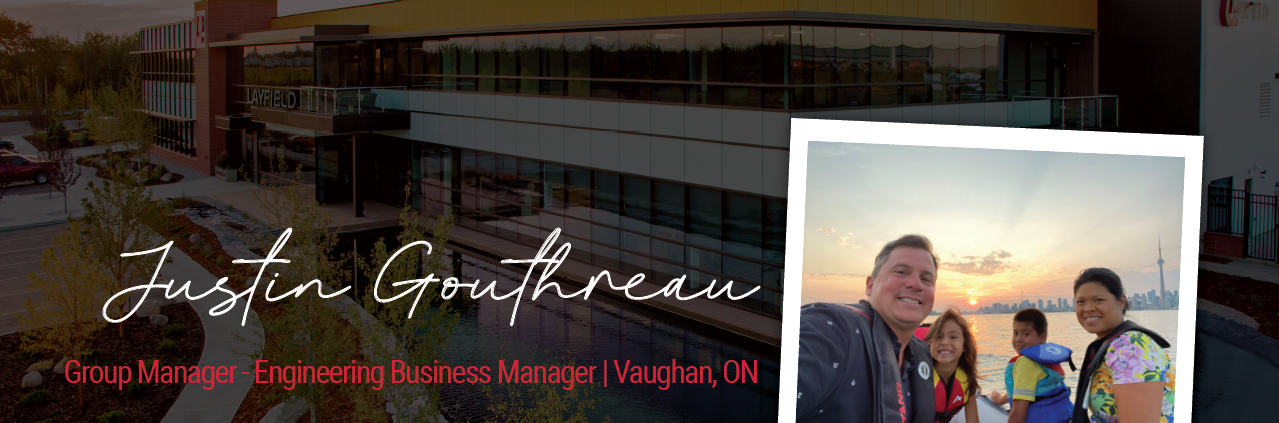
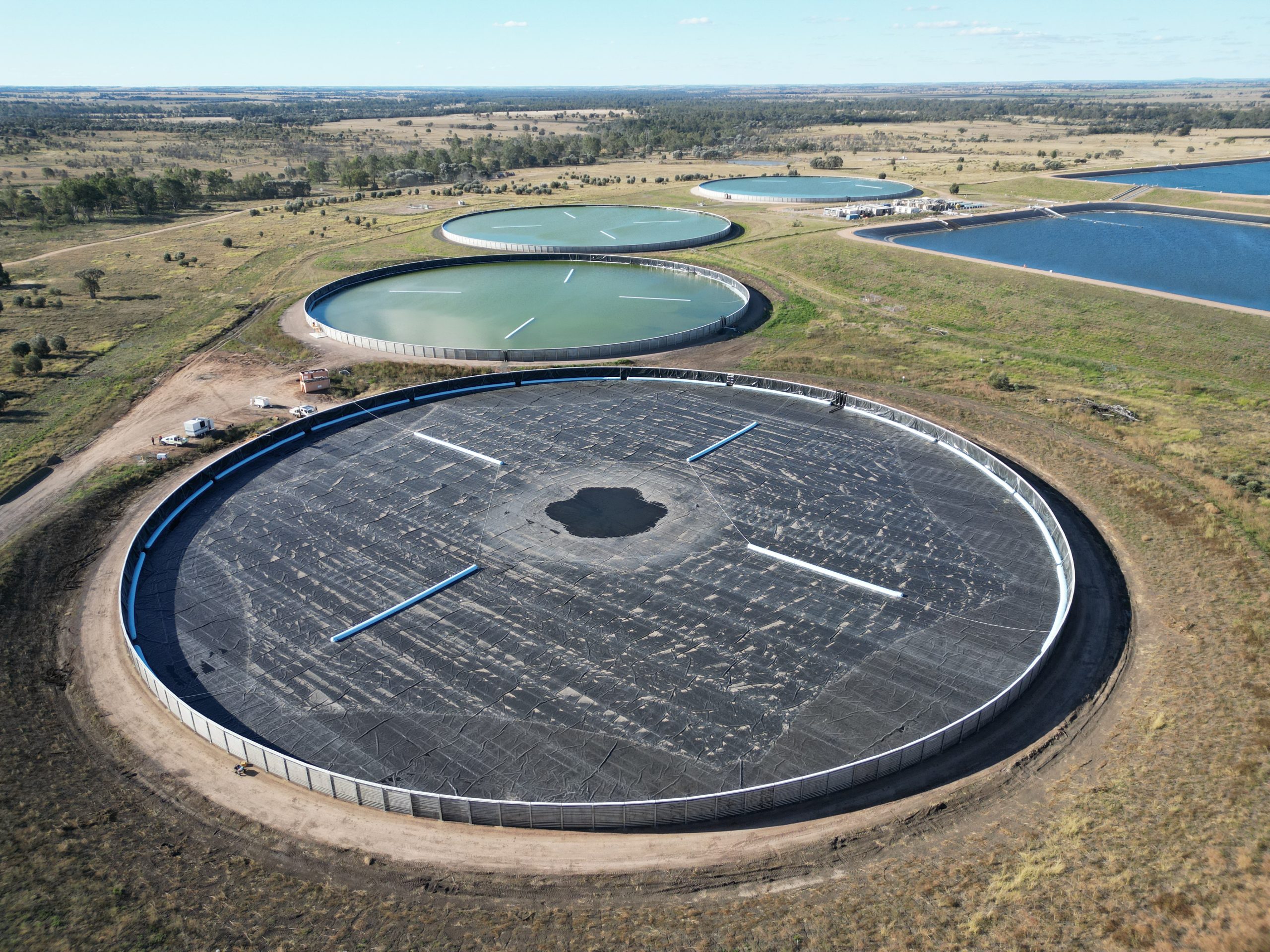
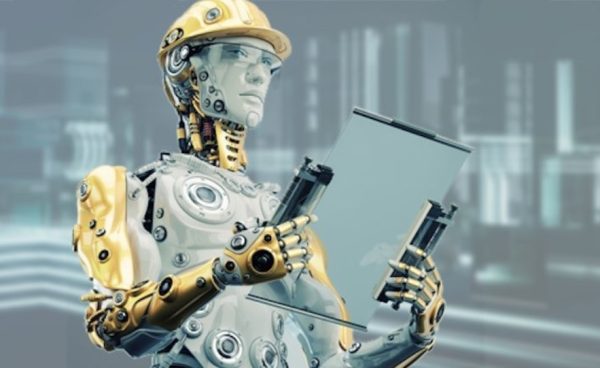
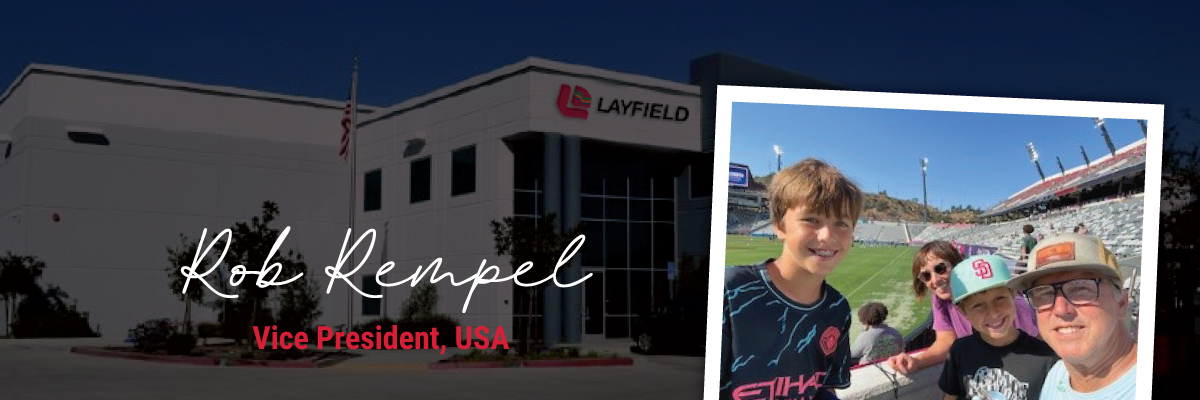
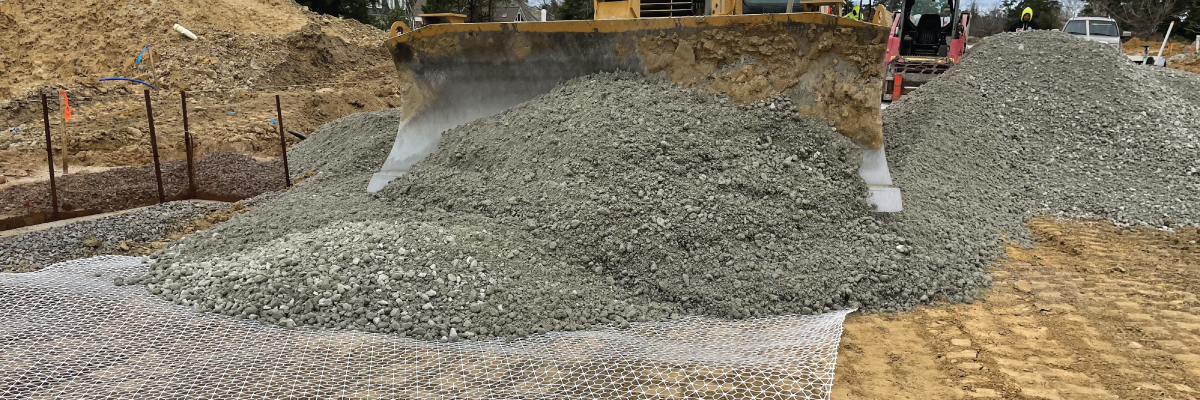
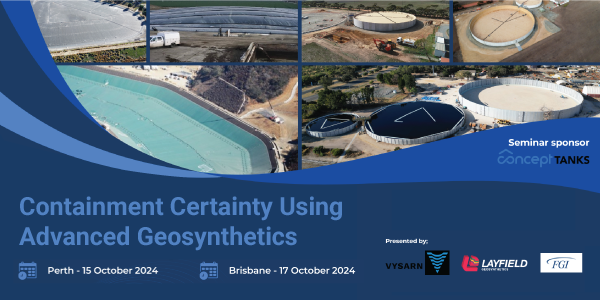