Written by Joshua Venters | Layfield Geosynthetics
The use of geotextiles has steadily grown over the past century. Geotextiles were initially derived from existing textiles readily available on the market, such as carpet back and upholstery fabric. Manufacturers have modified geotextiles to provide increased benefits to roadway construction. While there are two main types (wovens and nonwovens), there often needs to be more clarity about which product to use on your Jobsite. Common misconceptions about the functions of a woven geotextile vs. a nonwoven geotextile can often lead to added confusion. This tech note will detail the two main types of geotextiles and their functions.
Woven geotextiles:
First-generation woven geotextiles were made of slit tapes. Slit tapes are extruded flat yarns woven at 90-degree angles to yield a durable textile. Due to their wide smooth surface, they have very poor water permittivity and low soil interaction properties. These factors make them a poor choice for civil applications, especially in wet conditions.
Over time, the development of high-performance woven geotextiles has led to a more effective material. These developments have improved flow rates and higher interaction coefficients, making them more suitable for civil applications by providing separation, confinement, and reinforcement. They also allow for enhanced filtration and drainage.
Nonwoven Geotextiles:
Similar to wovens, nonwoven geotextiles are made using a synthetic textile. However, they have a more random structure produced by the interlocking of fibers. Wovens and nonwovens are used in similar applications, leading to confusion. The easiest way to identify the difference between a woven and nonwoven geotextile is by its physical attributes. Nonwoven geotextiles look and feel like felt, with the characteristic “fuzzy” look to the material.
When it comes to manufacturing a nonwoven geotextile, many different methods are used today. The most common manufacturing method is needle-punching. Needle-punched nonwoven geotextiles are made by taking a large number of small fiber fibers and using a barbed needle to interlock the fibers together. Nonwoven geotextiles provide separation, filtration, and drainage functions when used in a civil application.
The differences between woven and nonwoven geotextiles can be challenging when looking at material specifications. Generally, wovens have higher strength values, while nonwovens have higher flow rates and permittivity. The easiest way to distinguish the difference between the two materials is by starting with elongation. Nonwovens will have much higher elongation than woven. A nonwoven specification will list the elongation as greater than 50%, while a woven will be listed as between 5% and 25% if listed.
The following chart shows two examples of standard specifications for traditional and nonwoven materials. There are significant differences regarding their elongation and permittivity. However, tensile strengths are similar because they are manufactured from similar materials. All of these items are important to consider when choosing the correct type of geotextile for your application. It’s essential to ensure you use the right product for the right reasons.
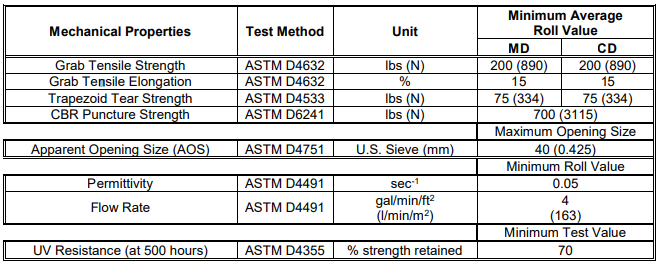
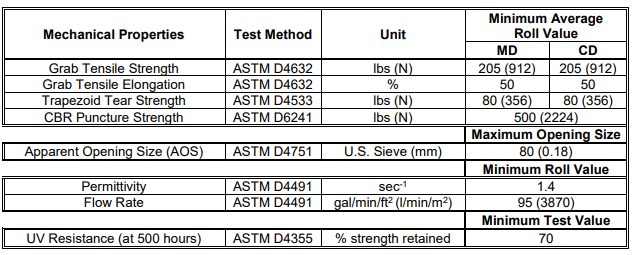
Weight of Nonwovens:
Another point of confusion is the weight of the differences between woven and nonwoven geotextiles. In both examples below, the weights are not listed. The weight of a woven geotextile is rarely specified. The reason is that they are typically used to provide separation and reinforcement and are not dependent on weight.
Conversely, the weight of a nonwoven geotextile is often specified, which is why you will typically hear or say, “I am looking for an 8oz, 4oz, 10oz, etc.” Nonwoven geotextiles have been measured by their weight for a long time, meaning the finished product would be 8oz per square yard. The remainder of the specifications, which include the strength, puncture, etc., would directly result from the product weight.
As the use of geotextiles has grown and developed, the manufacturing processes have also changed. Now, most nonwovens can be manufactured with a lighter weight and still achieve the same strength properties, reducing costs. There are always exceptions, such as in the case of using nonwovens as cushion geotextiles underneath geomembranes. In such instances, the puncture, weight, and thickness properties are more critical than the permittivity and strength properties.
Related Articles
View All News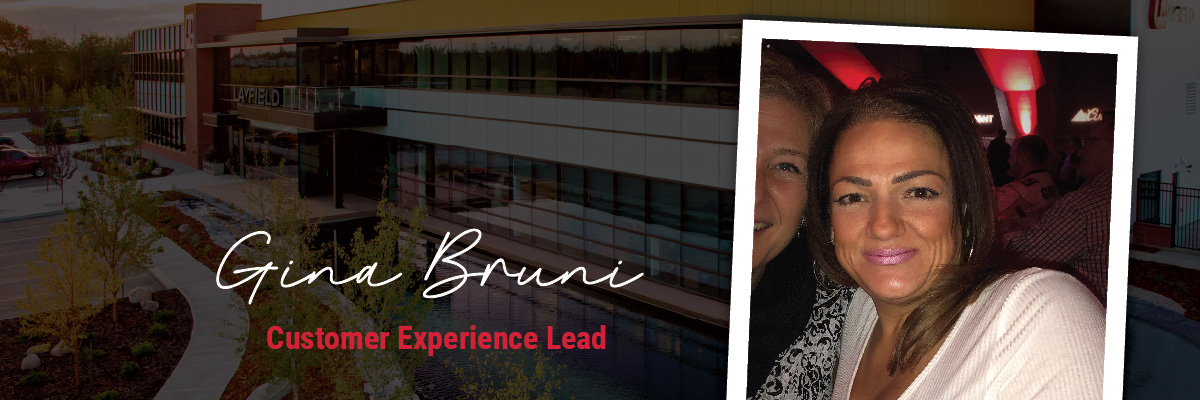
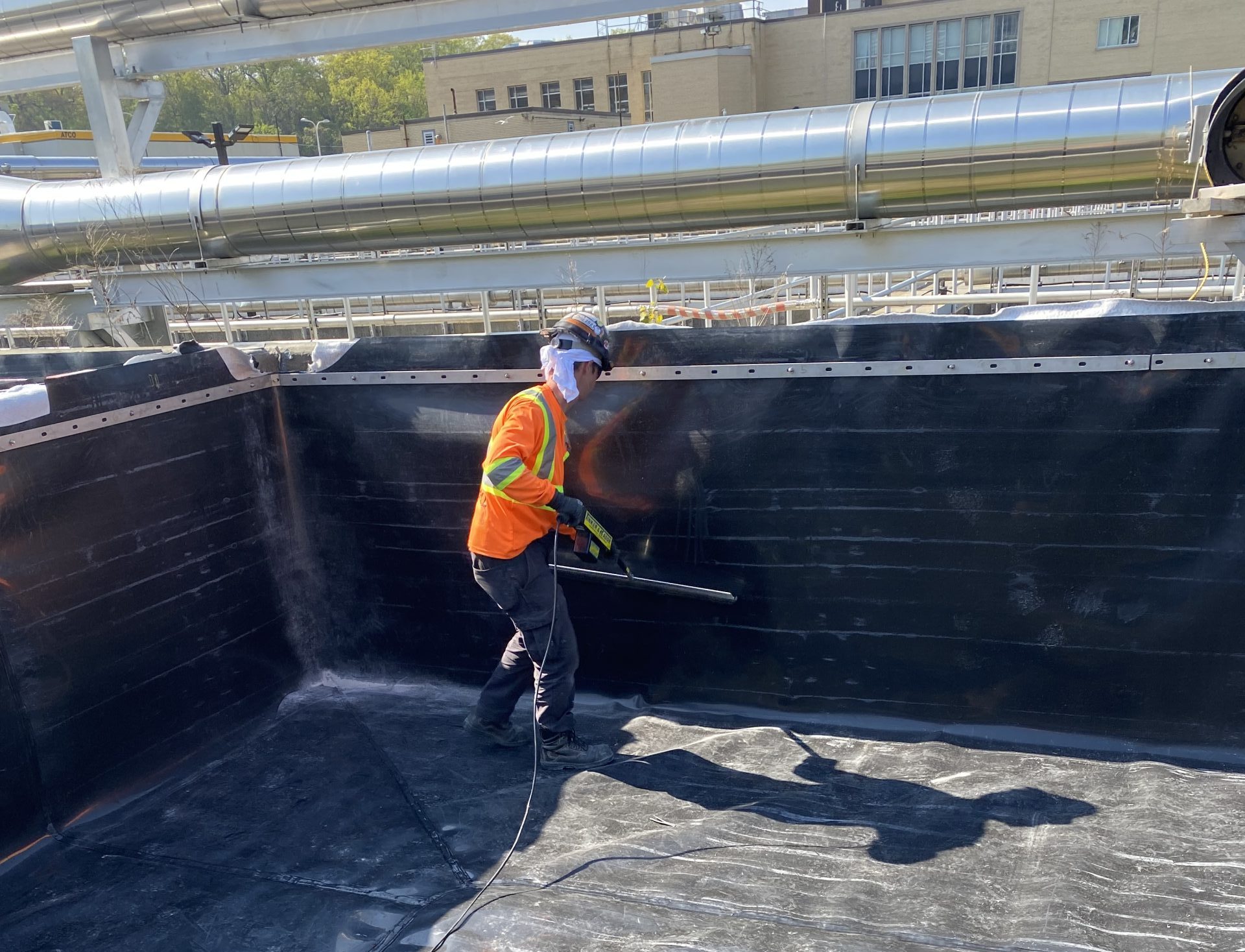
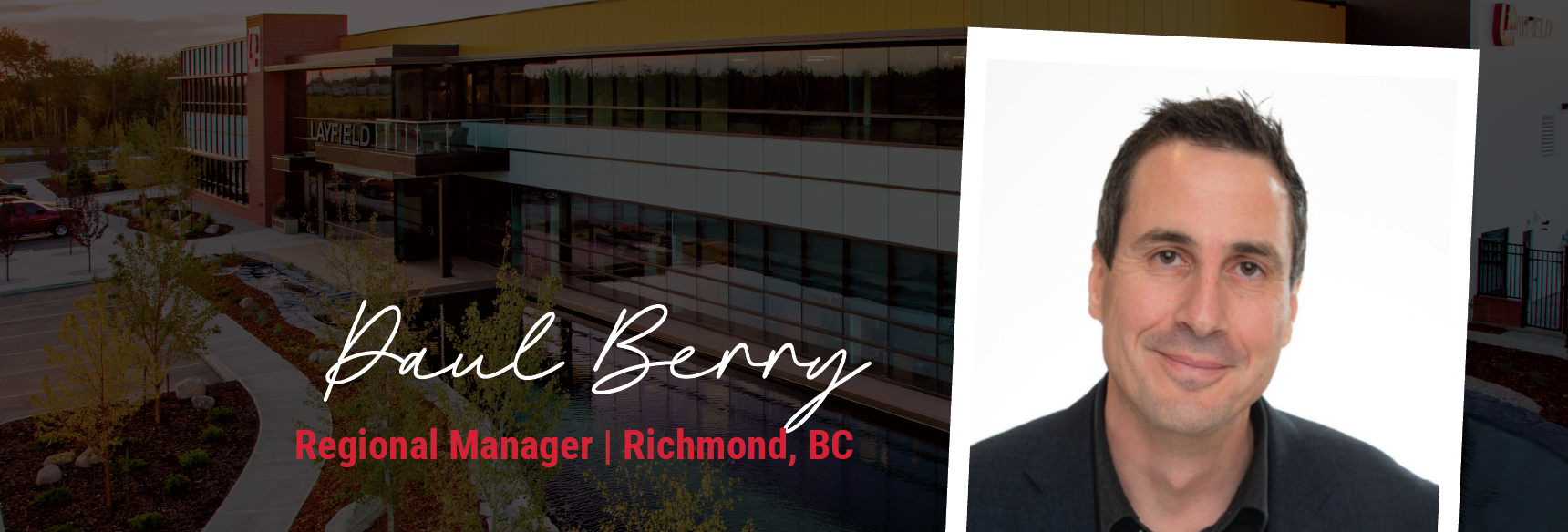
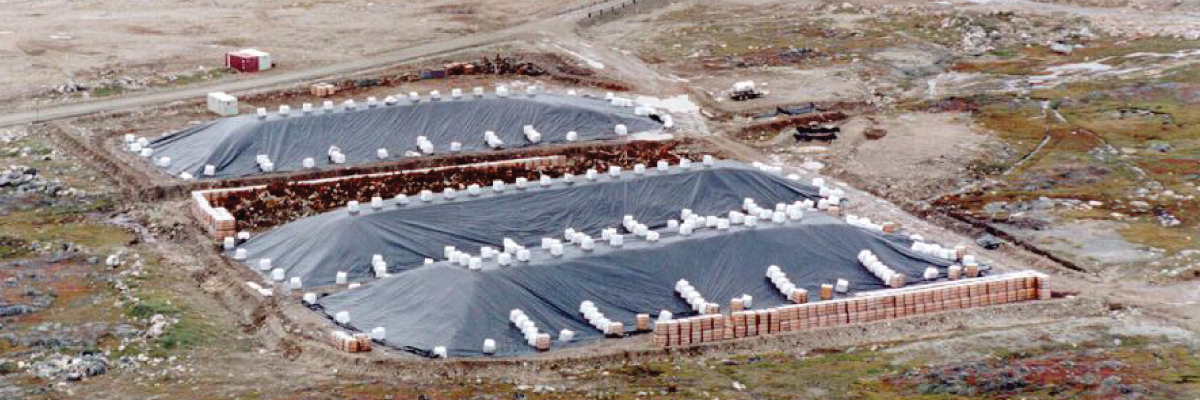
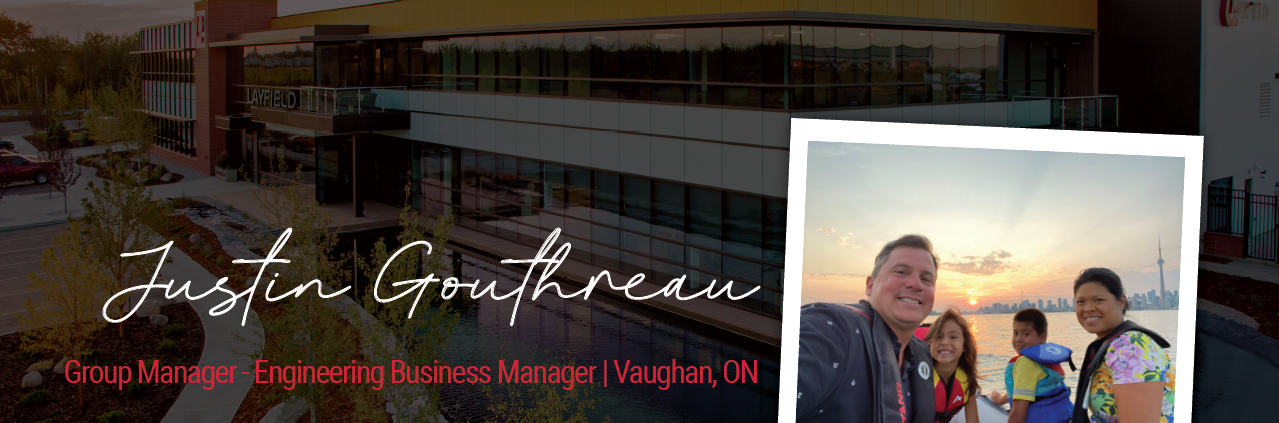
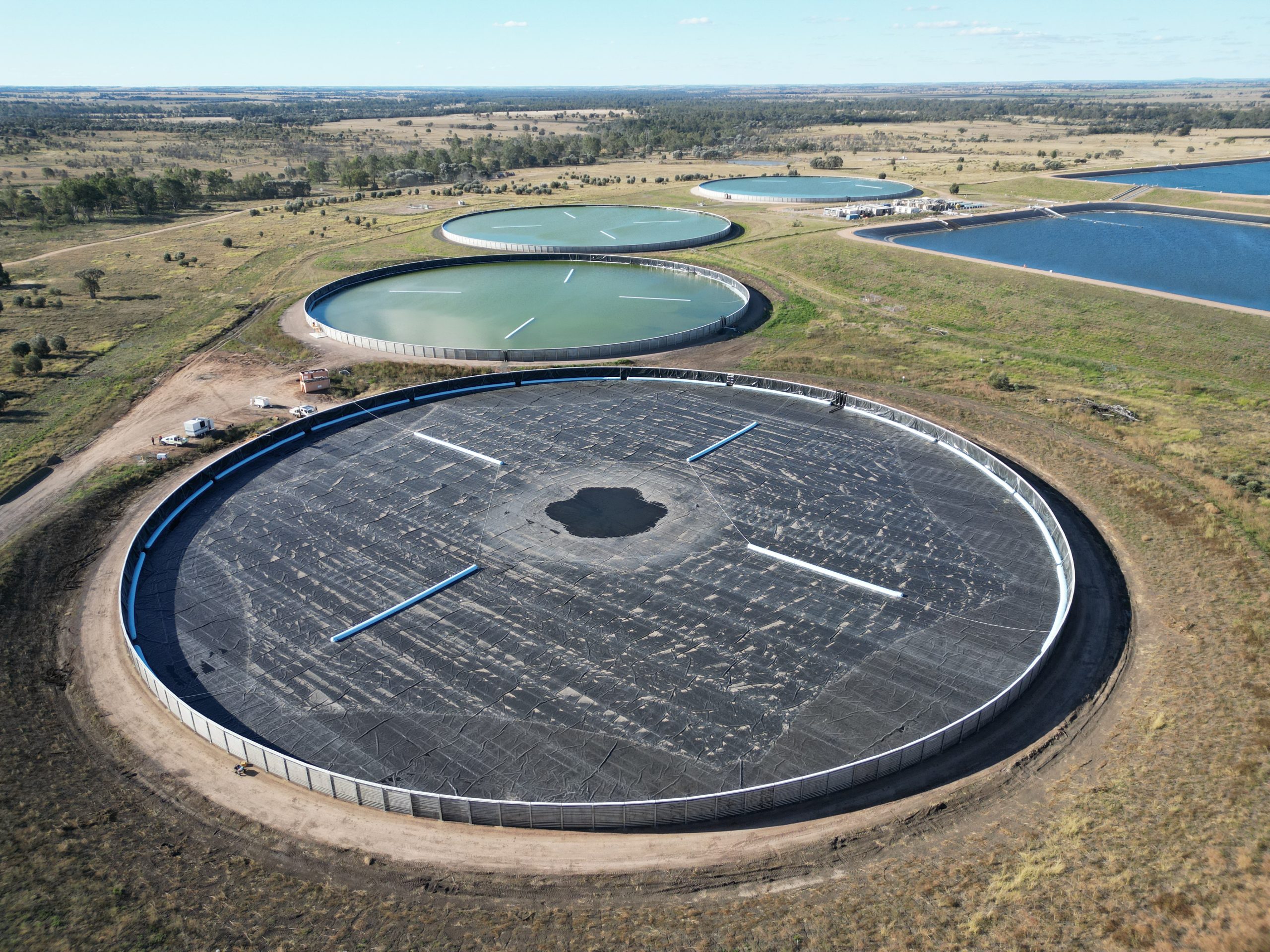
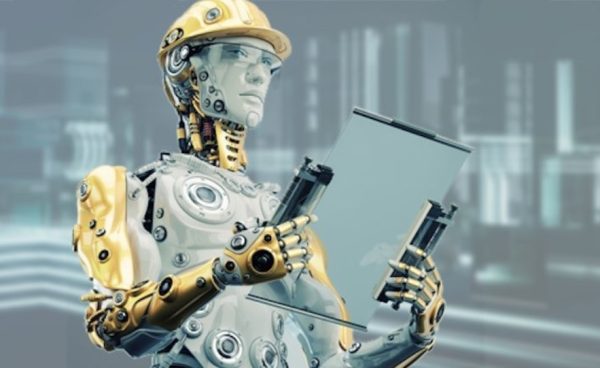
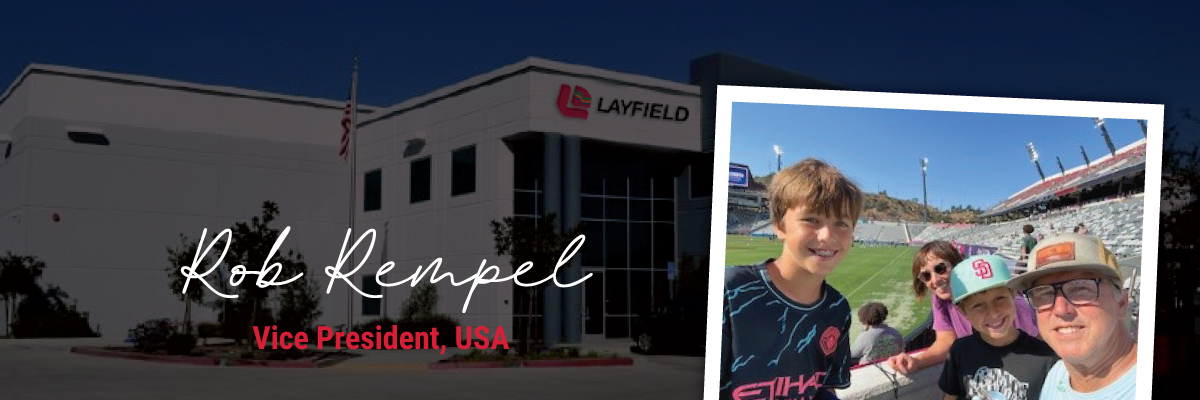
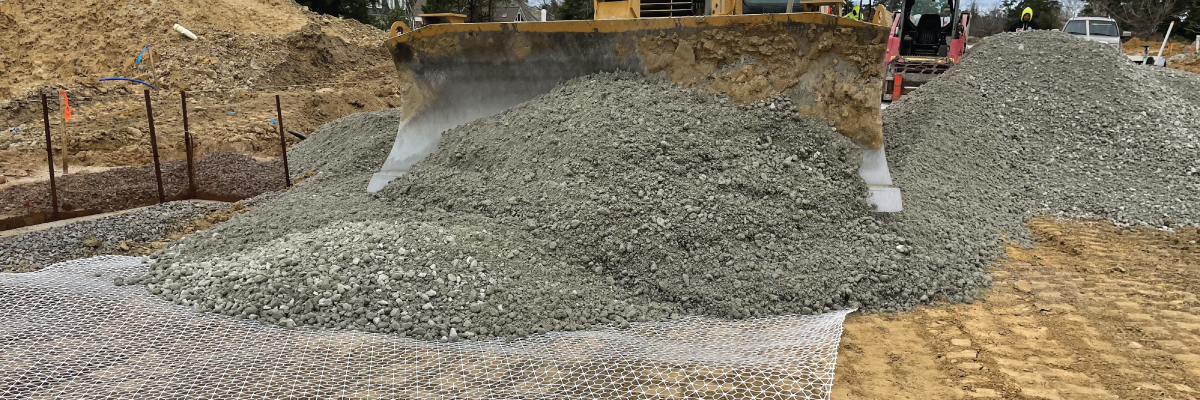
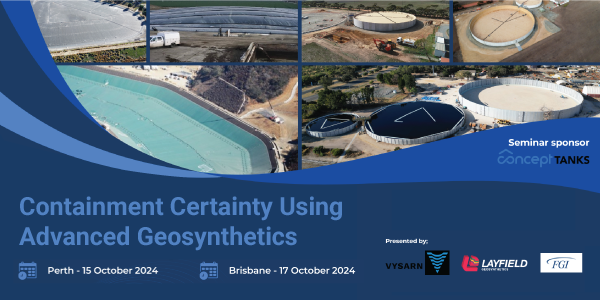